Q&A with Authors of Recent Plastic Plasmonics Publication
November 27, 2020
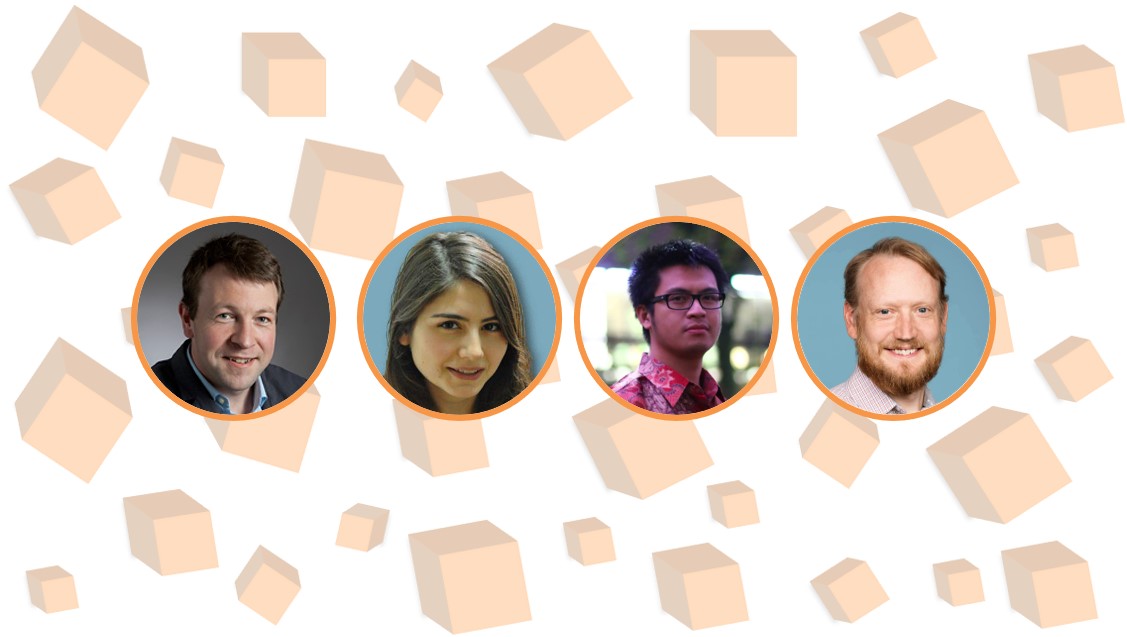
The research project was coordinated by Professor Christoph Langhammer at Chalmers University, and funded by the Swedish Foundation for Strategic Research (SFF). Insplorion was not involved in the project directly, but our research instruments and an early prototype of our gas-sensing platform were used for some of the experiments. While the results do not affect our hydrogen sensor project at the moment, they show promising new ways to produce gas sensor chips in scalable ways.
To share the results of this work with a wider audience and look at its potential implications for Insplorion, we sat down (virtually) with some of the authors for a deep dive Q&A.
PhD candidate Iwan Darmadi, the first author of the paper and the one responsible for evaluating the sensors at Professor Langhammer’s Lab at Chalmers.
Professor Christian Müller, head of the Müller group and responsible for overseeing the development of the hybrid nanocomposite.
Dr. Irem Tanyeli, responsible for coordinating the tests performed with Insplorion’s gas-sensing device.
Dr. Olof Andersson, responsible for the development of the gas-sensing device.
Background
The paper explores new ways of producing the materials for hydrogen sensors, namely colloidal plasmonic particles and their integration in a polymer (plastic) matrix to make hybrid nanocomposites, as well as fabricating and evaluating the performance of sensors made using these “plasmonic plastics”.
The research project that this paper has been produced by is funded by the Swedish Foundation for Strategic Research (SSF) and coordinated by Professor Christoph Langhammer at Chalmers. Its ultimate goal is the development of plasmonic hydrogen sensors using low-cost and scalable production techniques using polymer-based materials. This is done through a collaboration between three Chalmers research groups. The production of plasmonic and hydrogen-sensitive nanoparticles with uniform shape and size, using scalable chemical processes is done by Professor Kasper Moth-Poulson’s group. Professor Christian Müller’s group then takes care of identifying polymers with desired properties to create hybrid nanocomposite materials comprised of the nanoparticles synthesized by the Moth-Poulsen group and a polymer matrix. Once the nanocomposite is made, the Müller group uses various polymer processing techniques, such as 3D printing or melt-pressing, to produce “plasmonic plastic” hydrogen sensors. These sensors are then evaluated and characterized by the Langhammer group. In a last step presented in the publication, the best-performing nanocomposite produced by the Chalmers team was also integrated with Insplorion’s gas-sensing platform to evaluate it under more realistic conditions.
Q&A
What are the main takeaways of the paper?
Christian M.: A nanoparticle composite can function as a hydrogen gas sensor, even if the dimensions of the material are in the 100 micrometer range. The polymer provides an effective barrier to poisonous gases such as CO that would otherwise deactivate the sensor.
Iwan D.: The paper demonstrates a straight-forward and scalable way to produce plasmonic-plastic hybrid materials and advertises their use as active material in hydrogen sensors. We prove that it is possible to make a H2 sensor using a 3D printer and off-the-shelf fiber-optics.
In addition, our interdisciplinary team characterized this new class of “plasmonic plastics” extensively, which we believe is valuable for the R&D community and for further application development for these new materials.
Where did the idea for this project come from?
Christian M.: A lunch in restaurant Canyon at Chalmers.
Tell us a bit about the experiment conducted with the Insplorion device. What was the purpose?
Iwan D.: I am impressed with the device and that it can collect H2 sensing data with excellent signal-to-noise ratio. The data quality is already comparable to the setup I use in the lab and that use more sophisticated light sources and a spectrophotometer. It is fascinating to see how lab instruments can be replaced by Insplorion’s tiny device without compromising the sensing quality. In addition, the device is versatile: I can switch various transducers types conveniently, regardless if it is a nanofabricated or bulk-processed plasmonic plastic system.
Irem T.: The aim was to integrate the sensing material that Iwan et al. developed in the lab into our device to see how it would compare with experiments done using Insplorion’s X1 [research instrument]. The experiments were conducted as cycles of 10% H2, 0.5% CO, and their mixture, with synthetic air as the carrier gas. We were able to successfully obtain a reliable response with our device during cycles with H2 present and could also show that the plasmonic plastic is very stable over almost a year.
Olof you’ve been involved with developing the gas-sensing platform from the beginning. In fact, these tests were performed last summer, and the device has come a long way since then. Can you tell us a bit about the progress?
Olof A.: The basic principle of measurement is the same but a lot of improvements have been made since the measurements for this paper. Among the most important ones are a significant device cost reduction, an updated circuitry and a purposeful redesign of the case wherein the NPS sensor mount has been integrated in the electronics platform. All-in-all device performance has improved greatly. We are currently working on the NPS H2 sensor chip in our ongoing collaborative project with Chalmers, in which Powercell is also a partner.
Irem you’ve worked on both the NO2 project and the H2 project at Insplorion. How have they been different from your perspective?
Irem T.: NO2 was a bit like an untouched field for us. It brought many challenges and learnings to me personally. On the other hand, the H2 project is a field where the Langhammer group has full knowledge and experience. Even though both projects require quite different conditions, it was a very smooth and fast transition between the two. For example, the technical transformation we had to make to the gas-sensing platform was minimal to go from detecting NO2 to H2.
There are quite a few people involved across different disciplines. What are some challenges when coordinating between the various groups?
Christian M.: The challenge is to not stand in the way of the excellent students and postdocs who work in the project. Christoph has done an amazing job when it comes to coordinating the project as a whole.
Irem you started as a post-doc in a joint project with Insplorion and Chalmers and now you’re working at Insplorion. What are some differences between working in academia and industry that you have experienced?
Irem T.: Academia provides you a huge playground, you can play with any toy in any corner, great freedom. You can dedicate your time to solve any question you like. On the other hand, in industry you have to guide all your resources and efforts to reaching the final goal / product. On that way, there will be many obstacles that you cannot solve with your own expertise; for example finding users for the technology you’ve created. At that point you should involve others. That’s another main difference between academia and industry, in academia you can rather work in your small team but in industry you eventually have to work with bigger teams. Both might look like they are very different in their nature, but once they merge their visions and potentials we end up with very inspiring outputs as I experienced during my post-doctoral study with the collaboration between Chalmers and Insplorion.
What do you see as the next step forward?
Christian M.: The materials that we have developed do not respond quickly to hydrogen [compared to the previous work done by the Langhammer group]. The response time is limited by the slow diffusion of the gas through the polymer. This will be a tough nut to crack. We kind of want the polymer to be there, but then we don’t…
How do you see this impacting H2 sensing in the future?
Iwan D.: In recent years plasmonic-plastic hybrid materials have shown superior feature for ultrafast, sensitive and robust H2 sensors but it has been done with sophisticated-expensive equipment at clean-room facilities.
Our work opens the door to more cost-efficient hydrogen sensors by providing a cheaper and scalable way to produce the active sensing material. Furthermore, the material processing’s versatility provides a platform to design high-performance H2 sensors in the future.
What do the results from this paper mean for Insplorion?
Irem T.: The results from this paper definitely give us more confidence by showing that we are on the right track. The device development was initially started for air quality sensors but this study shows that our product has great potential to be adapted for various fields and applications. These collaborations like that always broaden our vision and boost our excitement.
A huge thanks to all the authors for taking the time to correspond with us and for answering our questions.
If there is something we missed or if you have any further questions, feel free to contact us directly info@insplorion.com.
/Maryam
Send us an enquiry.
We’ll get back to you as soon as we can.